29 July 2024
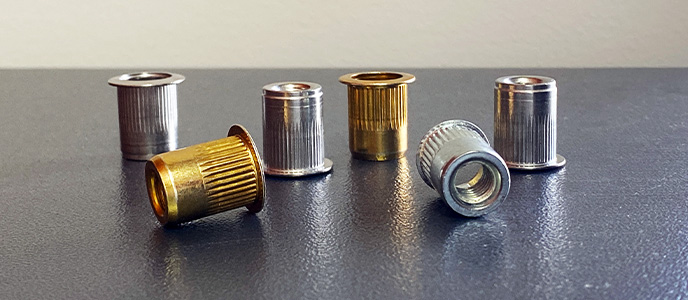
When it comes to securing joints in materials with limited access, the versatility and reliability of threaded inserts, also known as rivet nuts or nutserts, are unmatched. Here at Ovesco, we recognise the importance of these innovative fasteners for various industrial applications. Let's delve into the essentials of threaded inserts and why they are a vital component in your fastening toolkit.
What Are Threaded Inserts?
Threaded inserts are tubular fasteners designed to provide a strong, permanent threaded anchor point in materials that are too thin or brittle to support a conventional bolt. Commonly referred to as rivet nuts or nutserts, these fasteners are installed into a pre-drilled hole using a specialised tool that collapses the threaded inserts, forming a flange on the backside of the material. This process ensures a secure and durable thread for bolting applications.
Benefits of Threaded Inserts
- One-Side Installation: Threaded inserts can be installed from the front side of the workpiece without needing access to the back, making them ideal for blind applications.
- Material Versatility: Suitable for thin steel sheeting, tubular materials, and even lightweight materials like plastic and fiberglass.
- Post-Paint Installation: Threaded inserts can be installed after painting or coating, preserving the material's finish.
- Strength and Durability: They provide a resilient, permanent thread that withstands vibration and prevents unscrewing, especially when using hex-shaped or knurled body threaded inserts.
- Safety: Unlike welding, installing threaded inserts produces no toxic fumes, spatter, or base material distortion.
Types of Threaded Inserts
- Small Flange Inserts: Ideal for applications requiring minimal flange protrusion.
- Large Flange Inserts: Provide additional bearing surface and resistance to pull-out forces.
- Half Hex Inserts: Offer a combination of round and hex shapes for moderate resistance to spinning.
- Full Hex Inserts: Provide the highest resistance to spinning, ideal for demanding applications.
- Threaded Studs: These threaded inserts feature a protruding threaded stud, allowing for strong load bearing attachments in thin materials.
Installation Process
Installing a threaded inserts involves a few straightforward steps:
1. Thread the Threaded Inserts: Attach the threaded inserts onto the tool's mandrel.
2. Place and Swage: Insert the threaded inserts into the pre-drilled hole and activate the tool to compress the body, forming a flange on the blind side.
3. Secure and Release: The threaded inserts interlocks with the material, and the tool reverses out, leaving a firmly attached fastener ready for bolting.
Choosing the Right Threaded Inserts
Choosing the appropriate threaded inserts involves considering several factors:
- Thread Diameter: Match the threaded inserts’ internal thread size to your bolt specifications.
- Body Shape: Choose between round, hex, or threaded stud threaded inserts based on your application's requirements.
- Material Grip Range: Ensure the threaded inserts's grip range accommodates the material thickness.
- Head Type: Options include large flange, small flange, and countersunk heads.
- Material Type: Opt for steel, stainless steel, or aluminium threaded inserts depending on the environment and load requirements.
Tools for Threaded Inserts Installation
Depending on your application frequency and environment, you can choose from manual, air-powered, or cordless threaded inserts tools. Each type offers unique advantages, from cost-effectiveness and mobility to speed and ease of use.
Threaded inserts offer a reliable, efficient, and cost-effective solution for creating strong, permanent threads in thin materials. Whether you're working with steel, aluminium, or lightweight composites, these versatile fasteners ensure secure and durable assemblies. At Ovesco, we provide a comprehensive range of threaded inserts and installation tools to meet your specific needs. Trust us to help you find the perfect fastening solution for your next project.